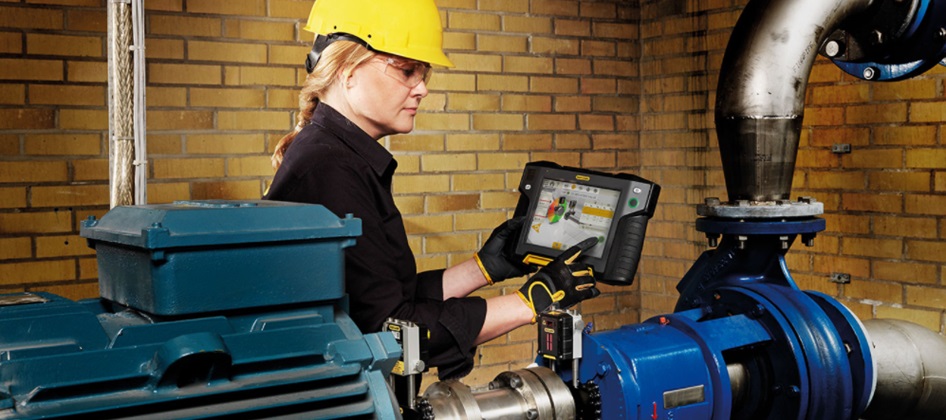
When looking at laser alignment systems, there are a number of reasons to use them within your work or industry as a versatile measurement tool that allows for analytical, detail orientated data to be fed back to you. This modern device ensures that all working parts of a machine are straight and secure before operating. As part of the maintenance process, without this insight, you could be at far more risk of failure during operation. This leads to downtime and slowed production, which could have been helped with a scheduled check with the right analytical device. Read on to find out why you might need to use these devices.
Fast And Accurate
These tools are multitudes faster and more efficient for accurate measurements, compared to the older dial gauges or straight edge methods. While the older methods can be highly accurate, they rely on the skill and trained eye of the user to be right. Whereas the modern method allows no room for error even if used by a less skilled operator. The average dial setup will not measure down to 0.001 mm, whereas a laser can.
Quick To Set Up, Easy To Use And Highly Reliable
These solutions for your mechanical analyses are quick to set up, easy to use and much more reliable than old technology. They rely on a skilled eye. The older options often require extensive experience and sometimes complicated calculations to effectively analyse your machines at work. There are tricks to the devices that only the experienced know, like a gauge device, will always drop slightly and be adjusted accordingly. When you have a more modern design in place you can get the most effective feedback in half the time.
Generate Reports With Results Straight Away
A modern alignment system like this makes it possible to generate quick and easy PDF reports directly from the instrument, which can detail the full rundown of specs for you to adjust as needed. The computer handles many targets and tolerances, and it is easy to interpret the results if you need to reassess the goal or levels. The ability to fully document the results gives better control over the machines and greater assurance as to the quality of your results. You can print out info from both before and after the process to show detailed readings on adjustments.
Gives You A Broader Picture
This tool allows you to easily detect possible soft footing and placement on the ground, as well as weak foundational support. Any dip in footing can cause movement during operation which in turn leads to a range of potential damage that could result in downtime. A large, vibrating machine must always be stable and steady on the ground to ensure safety.
The Speed And Precision Save You Money
The speed of use and the precision in alignment means that investing in a laser-based shaft alignment system usually pays for itself within 3-6 months. Not just the ability of the process itself, these solutions also save you costs of long-term maintenance as they greatly reduce the amount of damage that will occur organically through use. This ensures that you will have less downtime and fewer breakages.
A Disciplined And Repeatable Process
These modern tools make the process of measurement and correction much more disciplined and repeatable, with the same readings and adjustments being trusted as reliable data. With a repeatable process, you can ensure the reliability of the tool and the trustworthiness of the machines in use. Rulers and dial gauges are not sufficiently accurate for today’s modern machines and the room for error are enough to cause serious damage to expensive equipment. These tools give you the same reading on a machine, no matter operator or context.
Easy To Learn And To Use
One of the ideal things about these solutions is that you don’t have to be a specialist to get the correct results every time. This allows for more staff members to carry out these processes accurately, rather than needing specialist training. With a wireless display unit, you can follow the machine movement with live values at the points where you adjust the machine, not just where the dial gauges are mounted.
Laser alignment systems give you an accurate and eligible reading of machines to ensure that they are perfectly maintained. With all parts lined up correctly, you can continue operations without the worry of breaks or mishaps. When you can reduce the risk of damage you can save money and time. Contact us today to find out more.