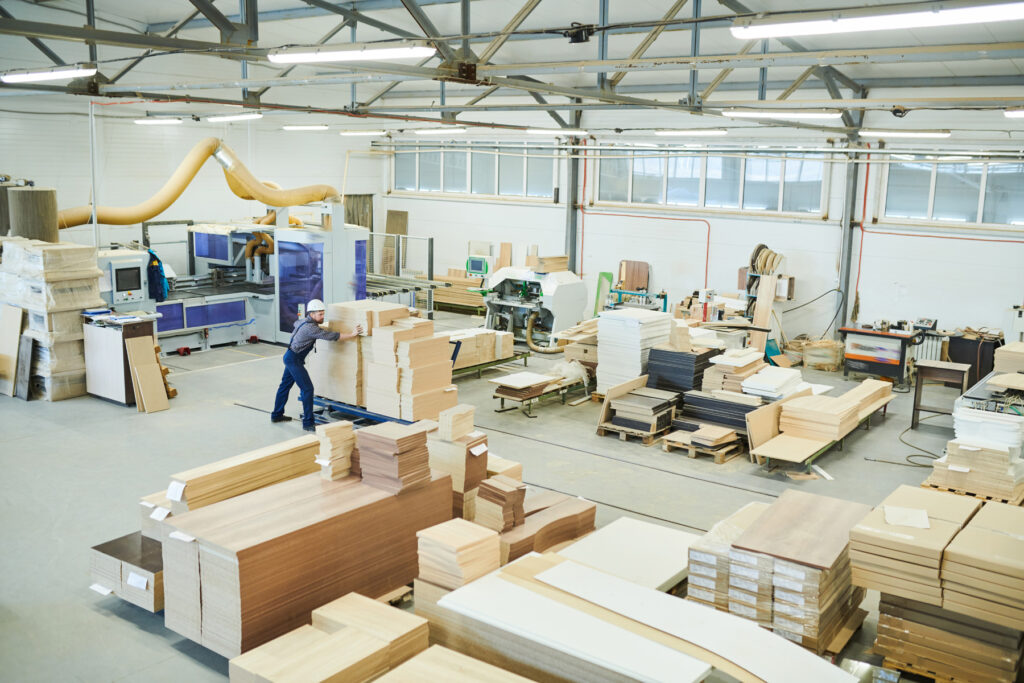
In the furniture manufacturing industry, achieving a flawless finish is critical for both aesthetic appeal and product longevity. One of the key factors that contribute to this high-quality finish is the use of powder coating ovens. These ovens play an essential role in ensuring that furniture pieces are not only visually stunning but also durable and resistant to wear and tear. By understanding how powder coating ovens contribute to the overall quality of furniture finishes, manufacturers can make informed decisions that enhance their product offerings.
Making Sure Heat Spreads Evenly for a Flawless Finish
A critical aspect of achieving a flawless finish in furniture manufacturing is the even distribution of heat during the powder coating process. Modern powder coating ovens are designed to ensure that heat spreads uniformly across every inch of the furniture piece. This even heat distribution is crucial because it allows the powder coating to melt and flow evenly, creating a smooth and consistent surface without any blemishes or imperfections.
When heat is distributed unevenly, it can result in issues such as orange peel texture, uneven gloss, or even areas where the coating fails to adhere properly. Industrial powder coating ovens are engineered to prevent these problems by maintaining a consistent temperature throughout the oven. This level of precision ensures that each furniture item receives the same high-quality finish, whether it’s a small chair or a large table, contributing to the overall quality and appeal of the final product.
Improving Color Consistency on Various Furniture Items
Color consistency is a key factor in furniture manufacturing, especially when producing multiple pieces that need to match perfectly. Powder coating ovens play a significant role in maintaining this consistency across different furniture items. By providing a controlled environment where the powder coating can cure uniformly, these ovens help ensure that the color remains consistent from one piece to another, regardless of size or shape.
A modern powder coating oven is equipped with advanced temperature control systems that allow manufacturers to set and maintain the exact curing conditions required for each specific coating material. This precision helps in achieving a uniform color finish across all pieces, reducing the risk of color variations that can occur due to inconsistent curing processes. As a result, furniture manufacturers can produce sets of furniture with a perfect color match, enhancing the overall aesthetic appeal and ensuring customer satisfaction.
Delivering Reliable Curing for Greater Durability
Durability is a crucial aspect of furniture quality, and reliable curing is essential for achieving this durability. Powder coating ovens are designed to provide the consistent and controlled environment needed for proper curing, which directly impacts the strength and resilience of the finish. Without proper curing, the powder coating may not fully bond to the surface, leading to a finish that is prone to chipping, scratching, or peeling over time.
Industrial powder coating ovens ensure that the coating cures at the optimal temperature and duration, allowing it to fully adhere to the furniture surface. This reliable curing process results in a finish that is not only visually appealing but also highly durable, capable of withstanding everyday wear and tear. For furniture manufacturers, this means producing items that retain their quality and appearance for longer periods, providing greater value to their customers and reducing the likelihood of returns or complaints.
Offering Customization Options for Different Coating Types and Textures
One of the significant advantages of modern powder coating ovens is their ability to accommodate various coating types and textures. Furniture manufacturers often require different finishes, ranging from smooth and glossy to matte and textured surfaces, depending on the design and customer preferences. Powder coating ovens are versatile tools that can be adjusted to meet these specific requirements, allowing manufacturers to offer a wide range of customization options.
By controlling the temperature and curing time within the oven, manufacturers can achieve different effects with the same base material. For example, a higher curing temperature might result in a glossier finish, while a longer curing time could produce a more textured surface. This flexibility allows manufacturers to experiment with different coatings and textures, creating unique and customized furniture pieces that stand out in the market. It also provides customers with more options, enabling them to choose finishes that best match their style and needs.
Minimizing Defects and Enhancing Surface Quality
Defects in the finish, such as bubbles, drips, or uneven surfaces, can significantly detract from the quality of furniture pieces. Powder coating ovens are instrumental in minimizing these defects, ensuring that the surface quality of the finished product meets the highest standards. The controlled environment provided by these ovens helps prevent common issues that can occur during the powder coating process, such as contamination, improper flow, or insufficient curing.
Modern powder coating ovens are equipped with features like air filtration systems and precise temperature controls that work together to create the ideal conditions for flawless finishes. By reducing the risk of defects, these ovens enhance the overall surface quality of the furniture, resulting in a product that is not only aesthetically pleasing but also built to last. For furniture manufacturers, this means fewer reworks, lower production costs, and higher customer satisfaction.