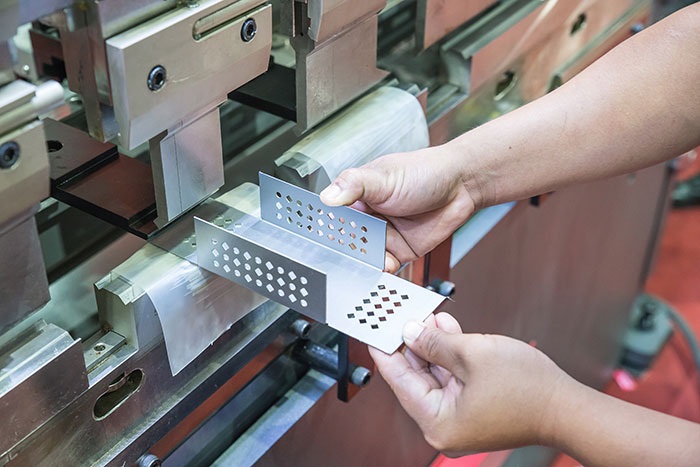
Sheet metal fabrication is a process that turns raw materials into manufactured components. It can be used for a wide variety of industrial projects.
It involves cutting, forming, welding, and assembly. These processes can be carried out in-house or outsourced.
Cutting
When it comes to what is sheet metal fabrication, there are many different methods of cutting and forming. How a piece of metal is cut or formed depends on the project.
The first step in a sheet metal fabrication process is to rough cut the metal. This means a significant section is cut from the sheet, making it easier to form later.
Another essential step in sheet metal fabrication is punching. This is when a metal piece is placed between two parts of the cutting process, a punch and a die.
This process is used to create slots and holes in the sheet metal. However, it can produce a lot of scrap material, so it is not usually a good option for small or medium-sized projects.
Other sheet metal fabrication processes include shearing and blanking. Shearing is a less precise way of cutting and is generally used for larger sheets of sheet metal that are often rolled. Shearing also produces scrap, but this can be minimized by clearing the area between the punch and the die.
Forming
Shaping is a process that involves applying force to a piece of sheet metal to deform it plastically. This material reshaping allows it to be bent or stretched into various complex shapes, creating solid structures without removing any material.
Sheet metal fabrication involves making sheets or coils of varying thicknesses from any metal, usually in thin pieces or rings called gauges. Steel, aluminum, stainless steel, and copper are the most common sheet metal materials in the fabrication industry.
Sheet metal is a versatile and inexpensive material used in many applications. It is also a malleable material, meaning it can be easily formed into almost any shape.
Welding
Welding is a process used to join pieces of metal at a high temperature. It’s a standard fabrication method in almost every industry, including construction.
In welding, a wire or electrode is fed into the joint to melt it with a filler metal. This filler metal is generally thinner than the base metal.
The heat from the arc melts the filler metal and makes it stick to the base metal. After cooling, the base metal is welded to the filler metal.
Welding can be a beneficial process for converting sheet metal into solid products for different uses. But it’s important to know which welding technique is best for your industrial application and how to use it effectively to get the most out of the process.
Assembling
Sheet metal fabrication involves altering flat sheet metal to produce various shapes and sizes. It is used by several industries, including aviation and electronics, to manufacture different products.
The first step in this manufacturing process is to take a raw piece of metal and shape it into the desired form. This is done by various methods, including forming, cutting, and joining.
Forming processes like stamping use two dies that press together a metal sheet to create the desired contours. These methods require custom equipment and tools, which can be costly and only feasible for large production runs.